How can companies build resilient Supply Chains?
Conventional operations and disconnected processes are no longer sufficient to adapt to global supply chain disruptions and will keep companies from harvesting the benefits that emerging technologies will bring in the near future. Supply Chain leaders need to stay ahead of these challenges and opportunities by creating and embracing strategies for supply chain digitization that will not only focus on cost efficiencies but also support faster and more informed decision-making.
Unreliable supply
Supply disruptions force procurement teams to spend extra time on price/contract management and researching and onboarding new suppliers, while expediting materials becomes more time-consuming. Without a lean supply chain approach, these issues can result in production impact, excessive inventory and inefficient use of financial resources. Including working capital optimization in digital inventory management further aligns inventory needs with cash flow.
Low visibility
Lack of visibility exacerbates issues since most companies are often unable to identify the root cause or even implement necessary corrective measures on impactful exceptions. To tackle this, Supply Chain leaders must prioritize achieving comprehensive end-to-end visibility that goes beyond engaging with tier 1 suppliers.
Lack of real-time data
Supply Chain leaders face significant challenges in achieving real-time updates due to the lack of modern and collaborative communication with their trading partners. Direct integration with suppliers is often too limited and legacy supplier portals are not built with real-time collaboration, real-time analytics and performance visibility in mind.
Digital Transformation Workshop
Quyntess offers you a complementary Digital Transformation Workshop, designed to make you aware of and prioritize your supply chain needs. This allows you to identify potential areas for improvement and develop quality improvement strategies and actionable plans to deliver better performance and strengthen your supply chain benchmarking.
Top priorities ranked by Supply Chain peers
If disruptions happen in real-time, then why is your supply chain still behind?
Recent studies show that only 31% of companies within multiple industries, including building materials, automotive, machinery & equipment, chemicals, and FMCG & retail, consistently utilize real-time data in their supply chain operations. Considering the persistent disruption and volatility, it is imperative for this statistic to improve.
In order to achieve efficiency, reduce costs, promote customer experience enhancement, and meet sustainability objectives, companies must be ready to embrace digital supply chain solutions to meet the industry goals for the next generations.
Reducing costs requires a strategic approach towards supply chain cost management. Effective cost reduction strategies play a crucial role in digital logistics. By implementing comprehensive supply chain cost analysis, companies can gain real-time insights and stay ahead of disruptions.
We have spoken to supply chain peers among our customer base and highlighted four essential priorities that should be at the top of every Supply Chain Leader's digital transformation agenda.
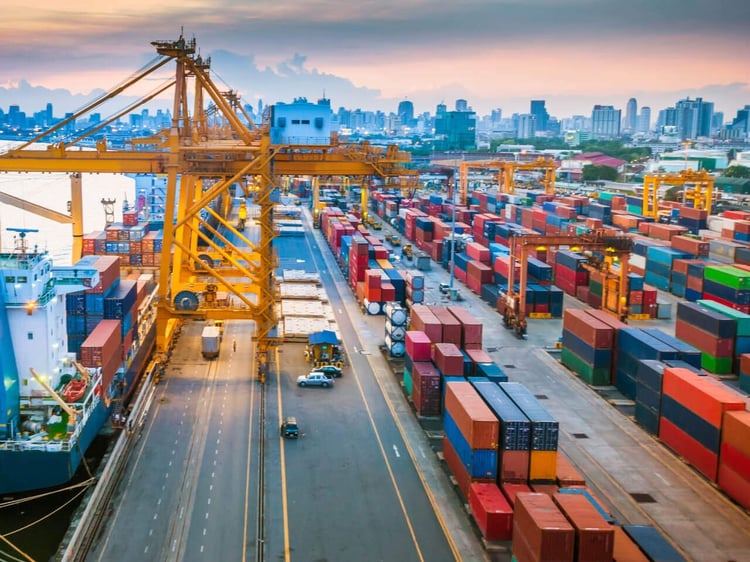
Interoperable supply chain
Proactive supply chain collaboration
Leaders are often unable to recognize the early signs of unforeseen events nor respond quickly to changing purchasing conditions, part shortages, compliance issues, and other supply chain shocks. Quyntess provides digital logistics solutions that enable real-time collaboration by extending communication and event management across all tiers of the supply chain, resulting in improved forecasting, shorter lead times, streamlined procurement processes, and increased productivity.
Operational execution performance
To guarantee stable production and reliable outbound deliveries, it is essential to have a solid inbound shipping process and strong dock-to-stock performance. Helping your suppliers to announce shipment details upfront and apply the correct packing material and barcode labels will improve inbound visibility and planning. Through the use of the Quyntess Supply Chain Management apps, integration of transport ordering helps increase speed and optimize supply chain efficiency.
Real-time insights and analytics
Real-time insights on key performance indicators, such as on-time delivery, stock availability, order accuracy, and production lead times are essential when working with a multitude of suppliers. Quyntess applies supply chain data analytics to seamlessly integrate and consolidate data from your ERP solution and the supplier network. This provides powerful insights that measure against supply chain efficiency metrics and the KPIs defined in the service level agreement.
High-performing Supply Chain leaders at a glance
“Digital supplier collaboration is one of several important initiatives that Global Supply Chain is taking to ensure even more reliable and sustainable supply of goods in the future, strengthening the competitiveness and flexibility of Vanderlande Industries as a leading player in the market."
Mart Corbijn van Willenswaard
Executive Vice President Supply
Vanderlande Industries
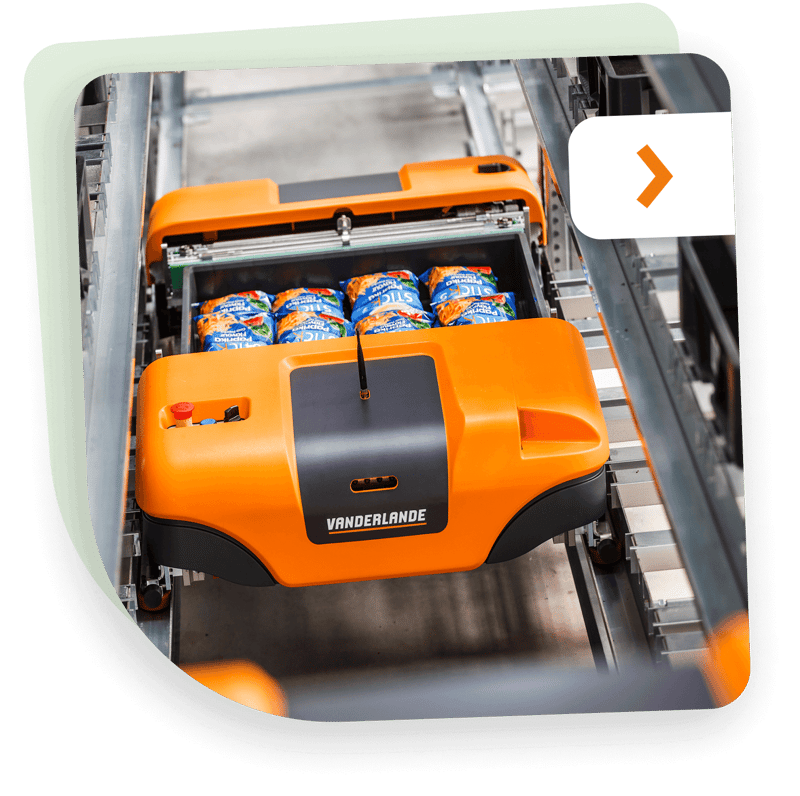

Pepsico UK

Ferrero
Most valued apps by Supply Chain Professionals
Introducing Supply Chain Apps capable of fulfilling all business priorities with seamless integration, enabling effective business process optimization.
With our commitment to incorporating composability into your digital SC strategy, we offer API-driven process integration between apps and external systems, providing the flexibility to focus on your specific supply chain priorities. Our supply chain optimization techniques cover your entire supply chain process, end-to-end, including e.g. forecasts, procurement, inventory, logistics, services, quality, and invoicing. All are accessible through a modern and global collaboration network.
By covering the complexity behind the screens of our applications and through our advanced data model layer, your teams can effortlessly navigate through a user-friendly interface to manage their roles in the supply chain. This results in enhanced access to real-time data, smarter performance indicators, improved AI capabilities, and a highly resilient supply chain ecosystem.
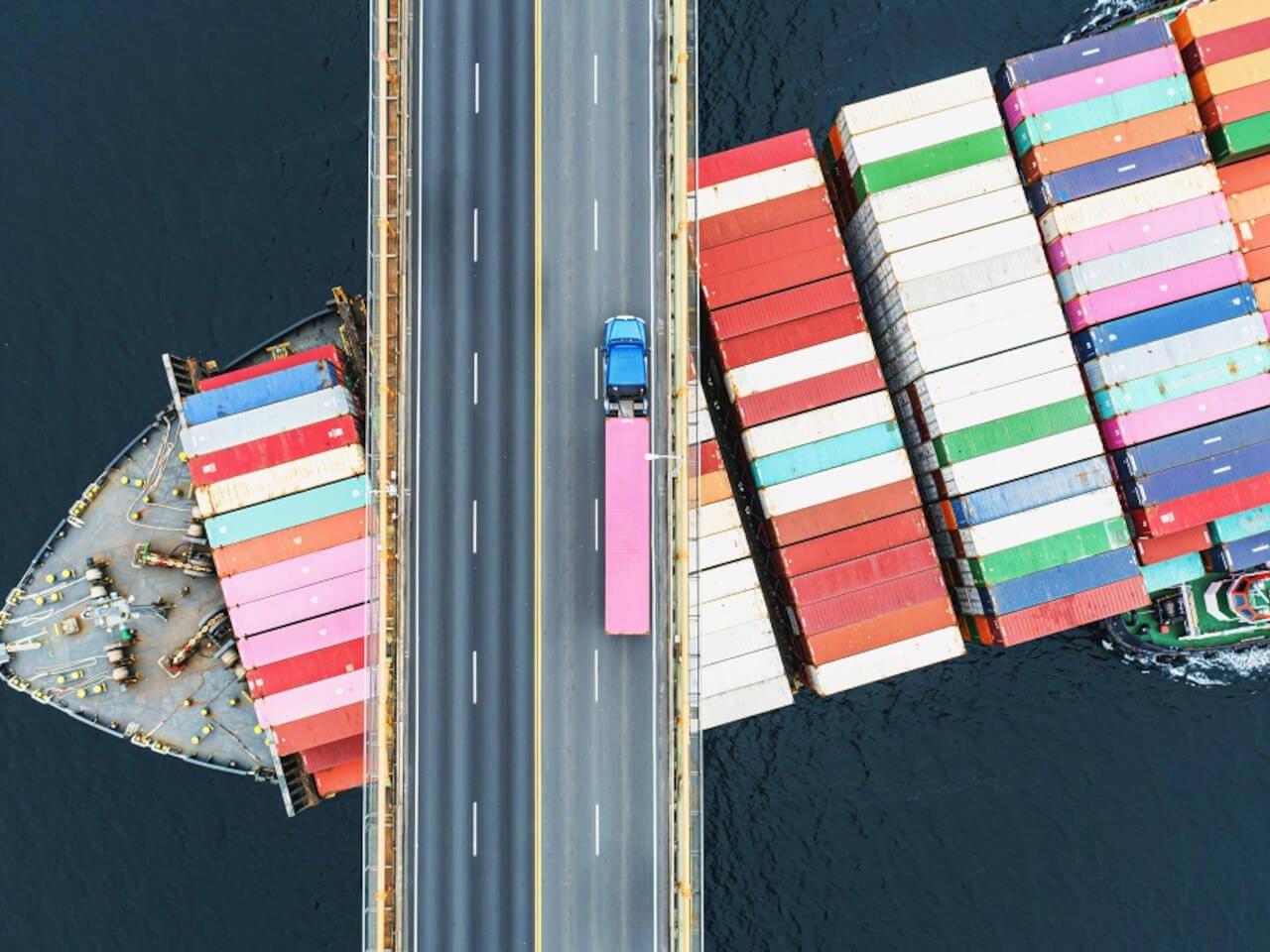

Forecast Collaboration
The Forecast Collaboration App allows collaboration between buyers and suppliers on developments in time-phased demand. With this app, both parties have access to the same demand & supply data and can set up a contract-based procurement process through digital workflow automation. Buyers and suppliers will be guided by the workflow to efficiently move through changes in the supply plan and the associated capacity from the supplier.

SCM Dashboard
The Supply Chain Management Dashboard is designed to better track and control collaboration with various suppliers and turn supply chain data into actionable insights. The app offers different screens and parameters that make it possible to get a single version of the truth about the performance of individual and/or all suppliers and other partners, creating a unique passage to your KPI metrics.

Logistics Collaboration
The Logistics Collaboration App simplifies communication and collaboration around the transportation process, enabling a continuous and orderly flow of real-time data between buyers, suppliers, carriers, and/or forwarders. The end-to-end integration of carrier information related to transport orders and freight costs allows automated invoice flipping across multiple connected ecosystems.

Shipment Collaboration
With the Shipment Collaboration App, suppliers can easily build shipments from open Order Lines or Schedules and announce these to buyers as well as to a logistic service provider. These Advance Shipment Notifications (ASNs) are your most effective control of actual supply performance. Advanced features are also available, such as "pack-and-stack", and data enrichment with serial numbers and certificates.

Inventory Collaboration
The Inventory Collaboration app is designed to improve visibility and automate replenishment (VMI/SMI) to increase availability in order to reduce safety stock throughout the supply chain. With this app, the procurement and repositioning of inventory are improved. Additionally, Inventory Collaboration is enabling omnichannel processing, faster actionability, and more optimal relocation decisions.
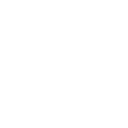
Could not find a suitable solution for your priority here?
The Quyntess app suite includes 13 powerful apps designed to enhance supply chain collaboration and optimize best practices. Learn more about each app and find a suitable integrated logistics solution to match your business requirements around order collaboration, co-manufacturing, product data management, product quality management and maintenance, or virtual payment cards.
Digital Transformation Workshop
Quyntess offers you a complementary Digital Transformation Workshop, designed to make you aware of and prioritize your supply chain needs. This allows you to identify potential areas for improvement and develop quality improvement strategies and actionable plans to deliver better performance and strengthen your supply chain benchmarking.
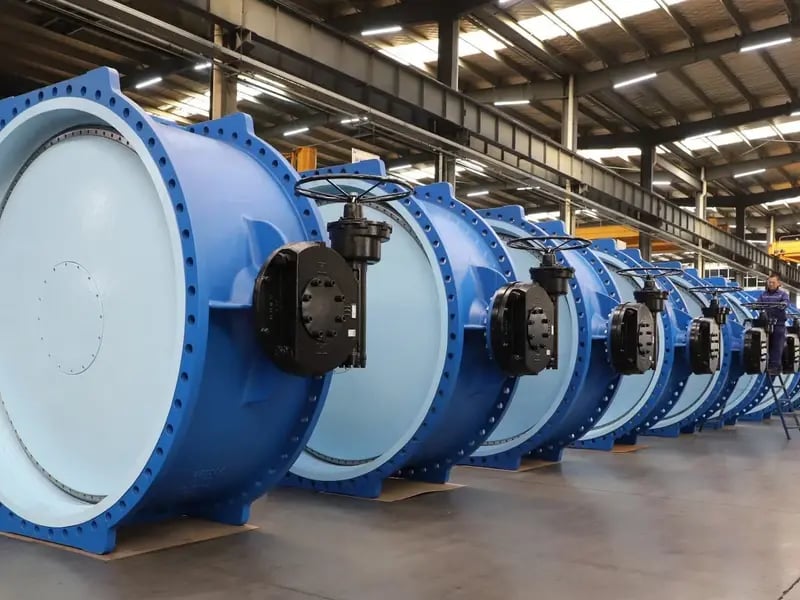
Tradeshift and Quyntess'
partnership enables
AVK to transform its
supply chain
With more than 100 companies and 20 manufacturing sites, AVK Group had to deal with a large global supplier base. Because these were predominantly Asia-based casting suppliers, AVK Group’s purchasing team’s day-to-day operations were impeded by cultural differences, different time zones, and language barriers.
Keep exploring
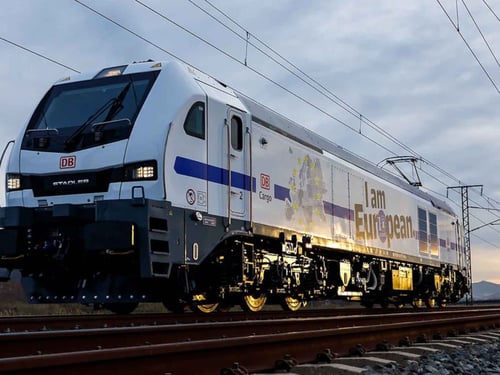
A €70 million support scheme to encourage...
The European Commission has approved under EU State aid rules a €70 million support scheme to encourage the shift of freight traffic from road to rail in the Netherlands.
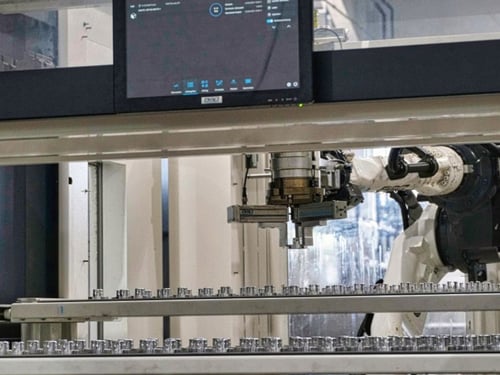
Do you trust your supply chain into the hands of...
I wanted to see with my own eyes how one of our customers manages to run 600 pallets per DAY through a subcontractor operation for repacking customer critical orders...
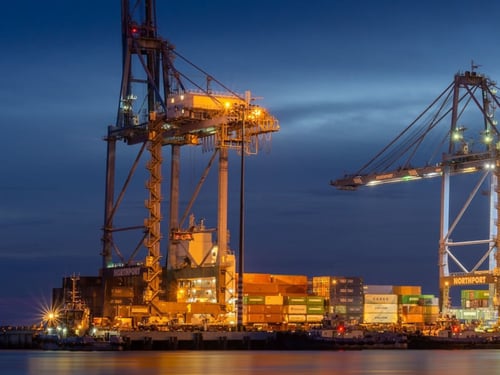
An integrated connector with Project44
Quyntess opted for an integrated connector with project44, the largest global network for order-level transportation visibility, to help consignors optimize their...
Do you have multiple priorities?
Discuss your challenges with us
Book a complimentary workshop with one of our experts to determine the top priority for your digital transformation. Already know your top priority or want to onboard new suppliers, get in touch so we can run a supplier check.
Frequently asked questions
Supply chain visibility is the ability to track products, materials, and inventory as they move through the supply chain. This includes real-time tracking of shipments and inventory. Supply chain technology and management software help achieve this visibility, enabling quick responses to potential issues. It supports supply chain risk management and enhances supply chain performance management.
Supply chain disruption occurs when the flow of products or services is interrupted, impacting production, sales or distribution. It can be by external factors or internal issues, preventing goods from moving smoothly. Supply chain risk management is crucial for building resilience. Supply chain innovation and supply chain automation may be needed to minimize delays and adapt to challenges
A resilient supply chain can quickly respond to disruptions and recover effectively. Key features include early risk identification, swift strategy adjustments, and recovery plans. Companies leverage supply chain performance management, supply chain digitalization, and supply chain integration to monitor risks and improve decision-making, ensuring minimal disruption and better process control
Digital supply chain transformation involves overhauling traditional supply chain management with modern technology. This includes innovations like supply chain digitalization, supply chain innovation, data analytics, and AI to create a resilient supply chain. By leveraging integrated logistics solutions and supply chain best practices, companies can achieve smarter, data-driven decision-making.
Real-time visibility provides live information about the status of goods in the supply chain. It helps track shipments and react to delays quickly. Using SC tracking solutions and supply chain technology, logistics can be monitored from start to finish. This visibility leads to fewer disruptions, while supporting supply chain performance management and supply chain risk management.